Case Study: Enhanced Automated Assembly
How One Company Achieved End-to-End Flexibility and Digital Control
Executive Summary
In 2012, Transformix Engineering introduced a new automation platform which offered a disruptive advance in high-speed assembly. Over the next several years, Transformix expanded the technology’s scope beyond the niche of continuous motion by applying its core principles to palletized processes. A particularly important development was the incorporation of “intelligent conveyance” into the platform. An evolution that brought an unprecedented combination of speed, flexibility, and digital control to automated assembly.
In 2018, Transformix launched the newest iteration of their platform, an initiative designed to repackage the technology into a set of configurable, plug-and-play modules. As part of this initiative, the company carried out a top-to-bottom reassessment of the platform’s architecture, and ultimately decided to switch to SuperTrak CONVEYANCE™.
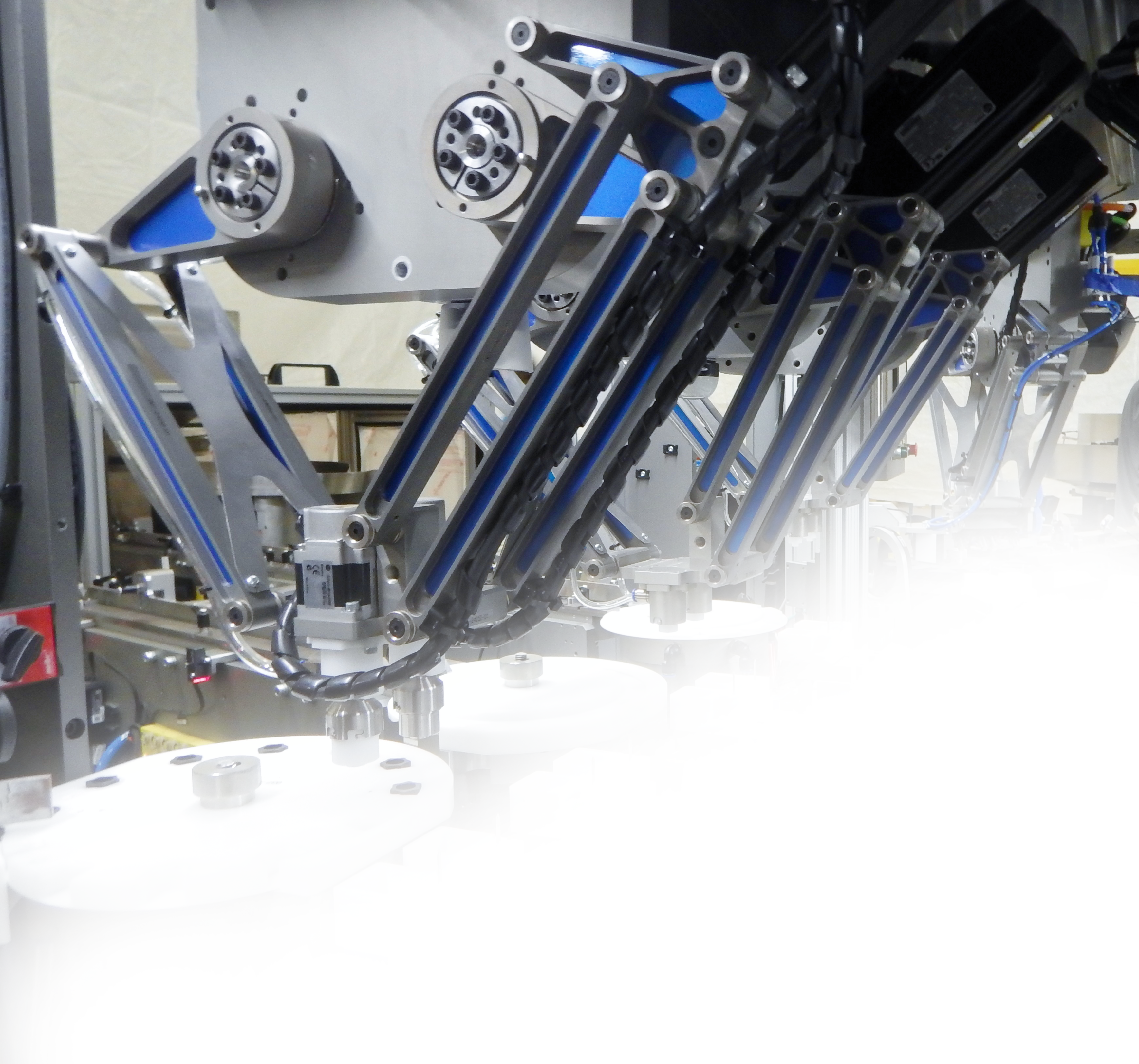
About the client
Similar to SuperTrak CONVEYANCE™, Transformix has a long history of innovation and continues to introduce new and exciting disruptive automation to factory floors across the globe. Transformix’s patented, groundbreaking technology allows automated assembly systems to serve as multi-purpose, reconfigurable assets. This eliminates non-value-added losses in order to yield high-performance systems that are configurable and do not require customization. With the goal of delivering an unprecedented level of standardization and versatility, Transformix continues to push the ongoing development of their platform by sourcing the best people, partners, and products.
The challenges
Finding the best conveyance product on the market that would support all the requirements of their platform was the main goal. The original conveyance platform being used brought challenges with high settling time, overheating, and frequent preventative maintenance. Transformix’s technology employs patented techniques that virtually eliminate non-value-added waste in automated assembly systems. This means work-in-process is brought in and out of the assembly workstations at rates that are often an order of magnitude faster than conventional palletized systems. This in turn places extreme demands on the intelligent conveyor, as shuttles are required to accelerate and decelerate rapidly and in quick succession, while nevertheless achieving high positional accuracy and repeatability.
The solution
Peng-Sang Cau, Transformix’s CEO, tasked her team to evaluate whether or not they were using the best conveyor available. Engineers quickly determined that they were not using the best conveyance platform for their application and that SuperTrak CONVEYANCE™ would eliminate the challenges they were experiencing with their current conveyor.
- The client benefited from the shuttles on the SuperTrak GEN3™ settling into position quicker and with greater accuracy and precision
- The client reduced time spent on preventative maintenance due to the plastic wheels on the SuperTrak GEN3™ platform
- The client no longer worried about overheating because of the built-in thermal monitoring offered by SuperTrak GEN3™
Automated Assembly Experience
Speed and accuracy were key drivers behind the success of the latest platform, however, they were not the only factors that differentiated the SuperTrak GEN3™ platform from its competitors, as Smith explained, “With our original conveyor, we were constantly facing challenges with heat dissipation. Our platform required pallets to operate at high duty cycles which caused our old conveyor to generate a lot of heat. We had to design costly means of dissipating this heat to avoid burning out the conveyor modules and to ensure a safe operating environment.”
Another problem with the original conveyor was the metal wheels on its shuttles. Not only were they noisy, but they also required frequent lubrication to prevent rust. In industries such as cosmetics, food and beverage, and life sciences, cleanliness is essential. This meant the machine would have to be taken out of production for maintenance and in essence, lowered valuable production time.
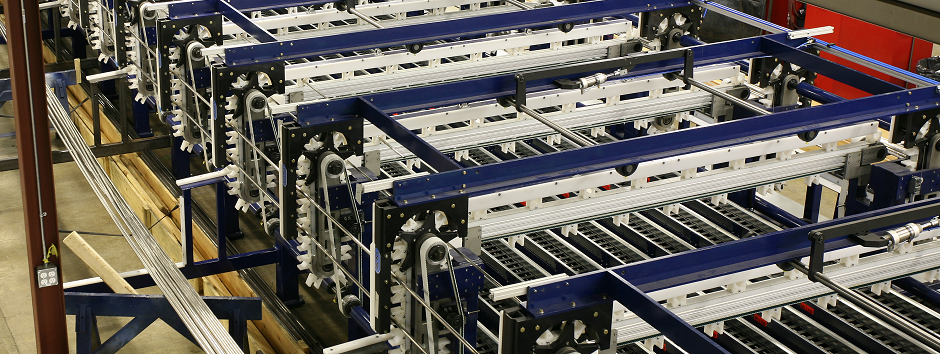
“Intelligent conveyance is essential to the end-to-end flexibility and digital control we offer,” explained Peng-Sang Cau, Transformix’s CEO. “But our original conveyor selection was based more on expedience and not on a thorough investigation of alternatives.”
The Results
“The combination of features offered by SuperTrak CONVEYANCE™ eliminated the challenges Transformix experienced with their original platform and better aligned with their vision of increasing plant efficiency, and decreasing wasted time, space, and resources.
Phil Munroe, one of Transformix’s senior mechanical engineers, prefers the SuperTrak CONVEYANCE™ platform due to the increased freedom it provides to overall assembly system design. “Our old conveyor had some limitations we always had to design around. As an example, its corner sections did not offer the same positional accuracy as its straight sections. We also had to be careful to avoid stopping the shuttles too close to the junction between two conveyor modules. Using the SuperTrak CONVEYANCE™ platform has eliminated these issues.”
Supported by a world leading automation company, the SuperTrak team understands the needs of a company like Transformix. The refinement offered by SuperTrak CONVEYANCE™ is evident, with a lot of built-in features and tools that make it easy to assemble, use, and service.
By aligning with a like-minded company and switching to the SuperTrak GEN3™ platform, Transformix was able to release a superior automation platform, allowing their customers to achieve better performance through high-speed operation, standardization, and versatility.
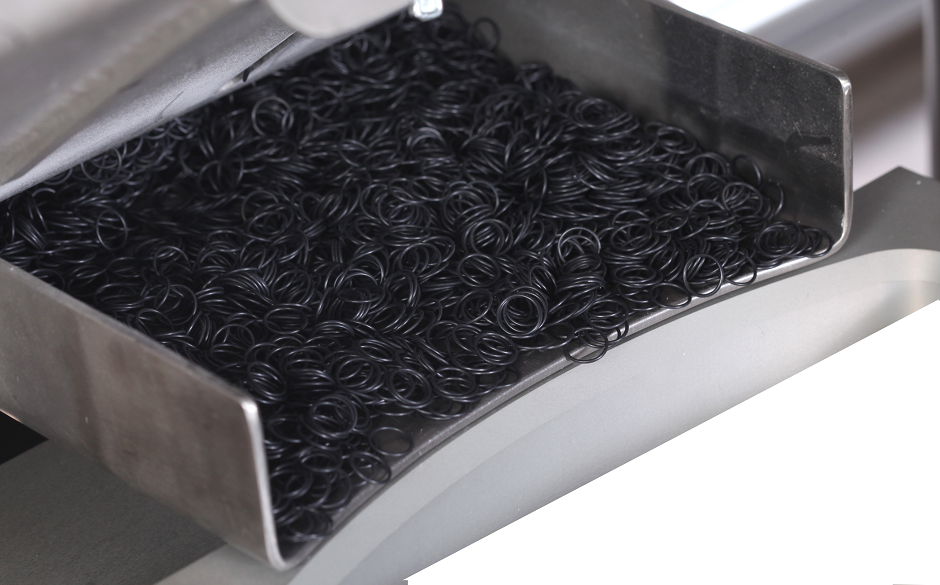
Application
Related Case Studies
Case Study
The Larisys Group – Case Study By watching this video, you will better understand the SuperTrak CONVEYANCE™ system, its capabilities, and how collaboration can lead to innovative solutions that can benefit the industry. Thank you for watching. The Solution The Results Related Case Studies
Case Study
Results Factory footprint reduction was the primary target of this implementation, however, the SuperTrak CONVEYANCE™ platform yielded better performance in the following areas as well: Related Case Studies
Case Study
Key Takeaways – The gradual deployment of their Smart Conveyance system – How their process improved at each stage of implementation – The results they achieved The Process Related Case Studies
Contact us
Complete the quick form to speak to a member of the SuperTrak team and discover how SuperTrak CONVEYANCE™ can be used in your automated assembly process.