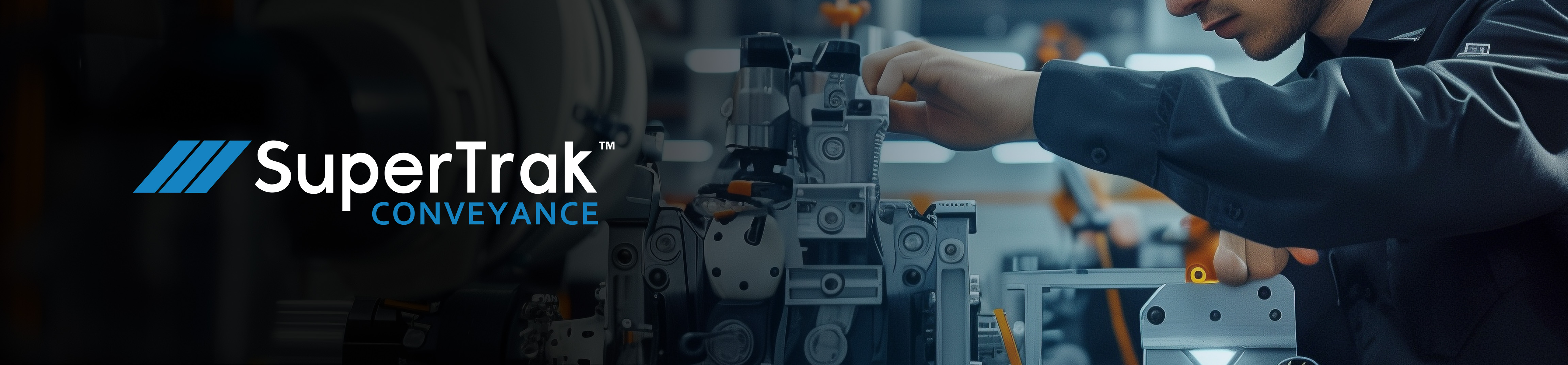
Optimizing Parts Changeovers
Changeovers are a challenge found on every machine designed to process several products. Industries like packaging, cosmetics, medical devices, automotive, and electrical devices often require changeovers between batches to produce anywhere from 2 to 100+ product variants on the same line.
Changeovers are commonly required to:
- Load various product sizes and shapes
- Position properly various products under stations
- Distribute different products to the appropriate processes
- Adjust the space between products to offload them in a package
- Manage production output on demand
In addition, handling of different trays may be required between machines, for which void elimination may be required.
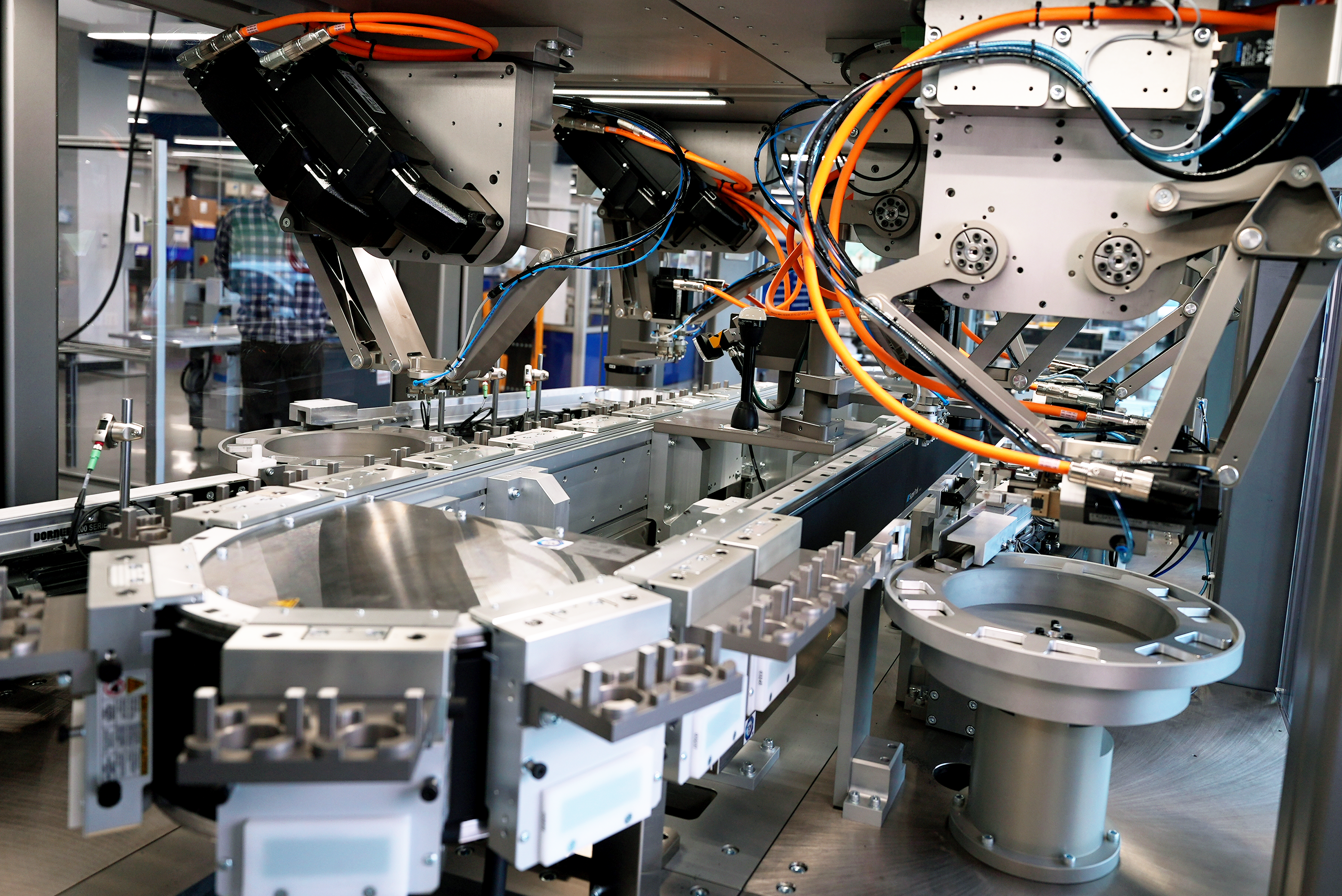
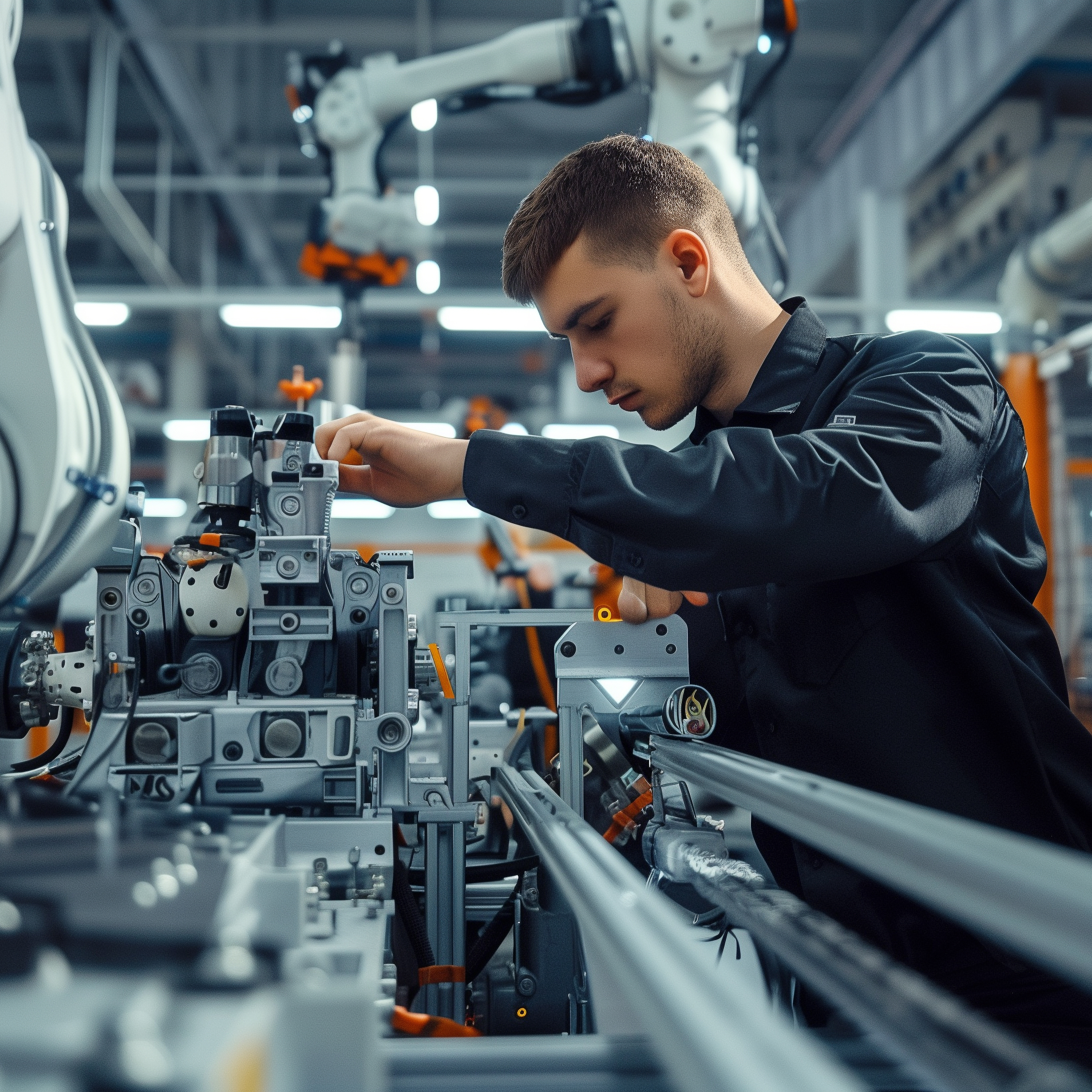
The challenges solved
The most common challenges related to changeovers are the cost and risks associated with mechanical and software changes. With daily or even hourly changeovers, the human factor becomes a critical part of the production’s success, and any issue can have a disastrous financial and customer-relations impact.
In addition, machines built to accommodate the production of several products are often mechanically more complicated and expensive. Finding a leaner solution for changeovers becomes key to building a viable production line within cost and space constraints.
Independent Shuttle Control
SuperTrak CONVEYANCE™ adds value to such applications by enabling complex motion that can vary depending on products and sometimes become part of the process, thereby reducing the need to change tooling or nests. Examples of independent shuttle control include adjusting shuttle targets differently for different products and using two coordinated shuttles to clamp products of various sizes without changing mechanics. As this motion is controlled by software, carrying or adding several products on the same line becomes possible with reduced efforts, and traceability of products becomes possible with the identification of each shuttle.